Cable Direction and Placement. Key Considerations
When planning the installation of floor-standing Low Voltage AC (LVAC) boards, contractors must carefully review the provided general arrangement (GA) drawings. This ensures efficient cable routing, compliance with installation requirements, and prevents costly mistakes on-site. Always consider the cable direction and size and type before ordering switchgear.
Where larger cables are required due to volt drop possibly using reduced palm lugs could get you out of bind. Ideally though the natural solution cost permitting would be larger devices fused down to accommodate the disparity in physical sizing.
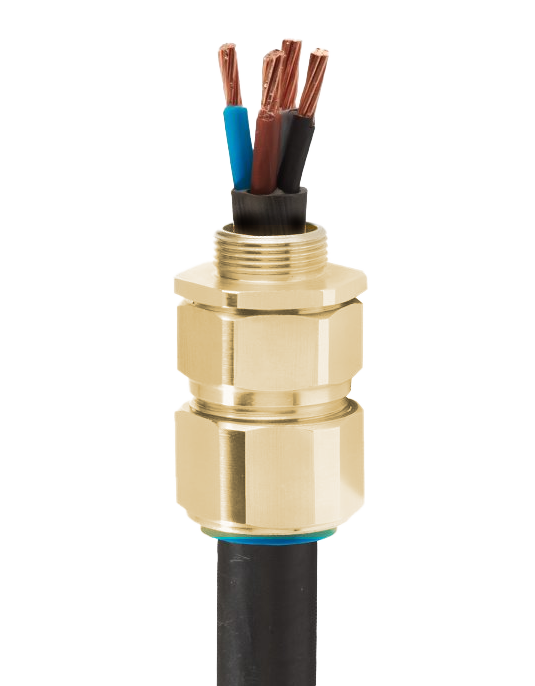
Understanding TOP and BOT Entry Configurations
We use the terms TOP and BOT to indicate the direction of incoming cables.
TOP Entry Boards
Incoming cables enter from the top of the board.
BOT Entry Boards
Incoming cables enter from the bottom of the board.
These configurations directly impact the space available for outgoing cables and the complexity of the installation.
Typical Cable Exit Configurations
TOP Entry, TOP Exit
Ideal for setups where both incoming and outgoing cables connect from above.
BOT Entry, BOT Exit
Commonly used where cables are fed from below, often via a cable trench or from an elevated building with outdoor or external circuits entering from below. The contractor must anticipate physical management of termination and cable direction / entry.
Mixed Configurations
- BOT Entry, TOP Exit
- TOP Entry, BOT Exit
These configurations are feasible but require careful planning due to restricted space caused by horizontal busbars.
Board Depth Options
Standard Depth
The standard LVAC board depth is 800mm, which suits most configurations.
Special Depth
For complex setups, such as mixed entry/exit configurations (TOP/BOT or BOT/TOP), a 1000mm deep board is available upon request to provide additional space for cable routing. Contractors should assess this need early in the planning phase.
Note: You could have 800m deep but the space for glanding due to obstruction of busbars will limit your glanding space. So if physical constraints dictate it 800mm is possible. If you are from for instance a utility organisation then your specifications team would need to acknowledge the deviations from standards.
Internal Raised Staggered Gland Plates for BOT Entry Boards
For BOT entry boards, we typically provide internal raised staggered gland plates for outgoing cables.
Benefits of Staggered Gland Plates
- Simplified Installation: Outgoing cables can be routed and glanded internally without requiring direct glanding at the base plate. Getting the termination of glands away from ground level.
- Improved Accessibility: The staggered design enhances cable management and allows secure installation even in limited spaces.
- Maximised Space Utilisation: This feature supports multiple outgoing cables efficiently, even in confined setups.
Drilling of internal plates
We should mention that the installer consider glanding areas and making the drill / gland point in a sensible place to allow for future glands. Offsetting ans sweeping gland cabling from the far right or left would be optimal to allow for additional glands to be added in the future. The staggered gland plates can be moved height wise but you need to consider they will be terminated and only cover a certain number of devices on the outgoing riser devices. Generally there are two for the span of either wardrobe (opposing riser / outgoing devices) or a single column. Looking a the GA will enlighten you further.
TOP entry boards
For TOP entry boards, the boards rely on gravity and grouping / turning in of cables onto the respective devices. Prior to tender should you need rear basket or tray added then this would be an extra but possible. Please inform us of the case upon submitting your information.
Frame and Gland Plate Material Distinctions
Painted Frames
The board frames are coated with durable paint, but will not withstand outdoor conditions to direct moisture over a prolonged period of time. If this is an outdoor installation then possible read the following for insight.
links.
Non-Ferrous Gland Plates
Both TOP and BOT gland plates are made from non-ferrous aluminum, providing:
- Corrosion Resistance: Ideal for environments with potential moisture exposure.
- Durability: Especially useful for installations where external air or humidity may be present, such as core-drilled concrete applications.
Contractor Responsibilities for Environmental Conditions
Indoor Installations
The contractor is responsible for ensuring that the environment meets acceptable standards for temperature and humidity.
Outdoor Installations
For outdoor installations, the principal contractor must size the enclosure appropriately and implement environmental controls, such as ventilation or HVAC systems, to maintain optimal conditions.
Failure to manage environmental factors could compromise the performance and lifespan of the board.
Importance of Space Around the Board
Clearance Requirements
- Front Access Boards: Require a minimum of 750mm clearance on each side. Rule of thumb leave at least the width of the widest door in front of the board. Stating the obvious of you have an 800mm door on an 800mm column you need that depth for the door swing as an allowance. If ACBs in cassettes are involved then the cassette depth extended plus space for lifting of ACB to an from the cassette unit.
- Rear Access Boards: Require 750mm clearance all around for full access and compliance with safety regulations.
Why Early Planning is Critical
Key Steps
- Analyse the GA Drawings: Review the GA to determine the best cable entry and exit configuration.
- Account for Depth Requirements: Decide if the standard 800mm depth is sufficient or if a 1000mm board is necessary.
- Assess Environmental Conditions: Plan for temperature and humidity control, particularly for outdoor installations.
- Ensure Adequate Clearance: Verify that the site meets the required space for safe operation and maintenance.
To wrap this up.
Proper planning of cable entry configurations, board depth (Some customer have fixed and approved designs so cannot be modified), and environmental controls is critical for successful LVAC board installation. By understanding material limitations and ensuring the right conditions, contractors can deliver a reliable, long-lasting system.
Disclaimer:
The information provided on this site is for general informational purposes only and may not reflect the most current regulations or standards. Legislation, industry guidelines, and best practices can change over time, and it is the user’s responsibility to research and ensure compliance with the latest requirements for their specific situation. Always consult a qualified professional for advice tailored to your project or application.