What is COSHH and Why Does It Matter?
The Control of Substances Hazardous to Health (COSHH) Regulations 2002 are designed to protect workers from exposure to hazardous substances in the workplace. These regulations apply to industries such as construction, healthcare, manufacturing, and cleaning services, where chemicals, dust, fumes, or biological agents are regularly encountered.
Failure to comply with COSHH regulations can lead to serious health risks, legal consequences, and long-term harm to employees. This guide explains key legal clauses, their practical implications, and how businesses can implement them effectively.
Full COSHH legal document: The Control of Substances Hazardous to Health Regulations 2002
Key COSHH Regulations and Legal Clauses
Regulation 6 – COSHH Risk Assessments
Employers must conduct and regularly review risk assessments to identify hazards associated with substances in the workplace. A risk assessment must be updated when:
- A new hazardous substance is introduced
- Workplace conditions change, affecting exposure levels
- An incident occurs, suggesting current controls are inadequate
- At least every 12 months as a routine review
A risk assessment must cover:
- Identification of hazardous substances (chemicals, dust, vapours, fumes, biological agents)
- Routes of exposure (inhalation, skin contact, ingestion)
- Who is at risk (employees, visitors, contractors)
- Control measures to reduce or eliminate risk
Employers should maintain a COSHH risk assessment log and train employees on workplace hazards and controls during induction and refresher training sessions.
COSHH Risk Assessment Guide: Managing risks and risk assessment at work – Overview -HSE
Regulation 7 – Controlling Hazardous Substance Exposure
Employers must prioritise prevention by removing or replacing hazardous substances with safer alternatives. If that is not possible, they must implement control measures such as:
- Engineering controls – Local Exhaust Ventilation (LEV), fume extraction, enclosed systems
- Workplace organisation – Reducing time spent in high-risk areas
- PPE (as a last resort) – Respirators, gloves, protective clothing
Testing and Re-Evaluation
- Ventilation systems must be tested every 14 months
- PPE effectiveness must be reviewed annually or upon damage
Workplace Exposure Limits (WELs): Workplace exposure limits – COSHH
Regulation 8 – Safe Storage of Hazardous Substances
Employers must ensure that all hazardous substances are stored safely to prevent exposure, spills, leaks, and contamination. Proper storage helps reduce risks related to fire hazards, toxic fumes, and accidental exposure.
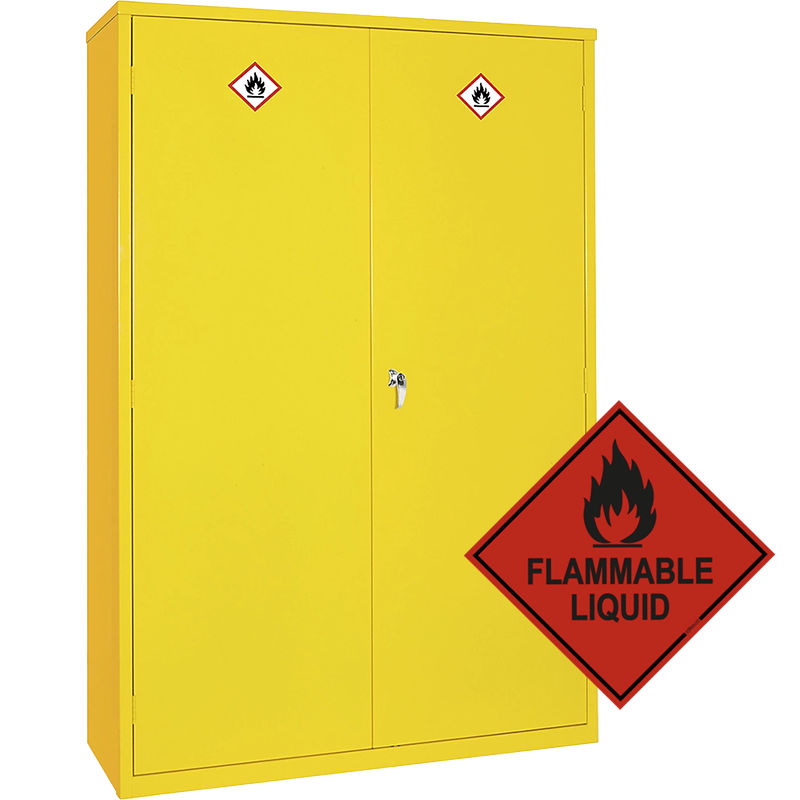
Key COSHH Storage Requirements
Segregation of Incompatible Substances
- Store flammable liquids separately from oxidisers (e.g. petrol and hydrogen peroxide must not be stored together).
- Keep acids and alkalis in separate containment areas to prevent dangerous reactions.
- Identify all reactive substances and ensure proper separation based on Safety Data Sheets (SDS).
Use of Correct Storage Containers
- Always store chemicals in their original, clearly labelled containers.
- Never decant hazardous substances into unmarked or inappropriate containers (e.g. food containers).
- Ensure lids and caps are securely sealed after each use.
Ventilated and Fire-Resistant Storage Areas
- Store volatile chemicals in well-ventilated areas to prevent fume buildup.
- Use fire-resistant cabinets for flammable substances such as solvents, thinners, and industrial cleaning agents.
- Ensure gas cylinders are stored upright, in well-ventilated spaces, and securely fastened to prevent tipping.
Temperature Control and Spill Containment
- Keep chemicals at safe temperatures, avoiding exposure to heat sources.
- Use bunded storage areas (with raised edges or trays) to contain potential spills.
- Implement spill control kits nearby to address leaks or accidental releases immediately.
Access Control and Signage
- Restrict access to hazardous storage areas to trained personnel only.
- Use clear hazard signage (e.g. flammable, corrosive, toxic) on all storage units and areas.
- Ensure an up-to-date inventory of hazardous substances is maintained at all times.
Regular Inspections and Maintenance
- Storage areas must be inspected at least every six months for leaks, corrosion, or signs of damage.
- Expired or unused chemicals must be disposed of safely in accordance with Regulation 13.
Practical Implementation
Employers should establish dedicated storage areas, provide training on safe handling and storage procedures, and ensure that SDS (Safety Data Sheets) are available for all hazardous substances on-site.
More information on COSHH Storage Guidelines:
Control of Substances Hazardous to Health (COSHH) – HSE
Regulation 9 – Maintenance and Testing of Control Measures
Employers must ensure all safety equipment is maintained and tested at specified intervals to remain effective. This includes:
- LEV Systems: Thorough examination at least every 14 months
- Respiratory Protective Equipment (RPE): Checked before each use, with fit testing for new employees and annual retesting
- Chemical storage cabinets: Inspected every six months to check for leaks or contamination
Maintain a testing log and set up automatic reminders for re-testing equipment. Employees should be trained to report malfunctioning or damaged safety controls immediately.
HSE Guide on LEV Testing: https://www.hse.gov.uk/lev/testing.htm
Regulation 10 – Monitoring Exposure to Hazardous Substances
If hazardous substances exceed Workplace Exposure Limits (WELs), employers must:
- Conduct air monitoring tests at regular intervals (annually for known risks)
- Keep exposure records for at least five years (40 years for carcinogens)
- Reassess if work processes change or new risks emerge
If monitoring indicates rising exposure levels, employers must act immediately—improving ventilation, adjusting PPE requirements, or modifying work processes.
Workplace Air Monitoring Guidance: Monitoring the control of exposure to hazardous substances
Regulation 11 – Health Surveillance for At-Risk Workers
Employers must implement regular health checks for employees exposed to hazardous substances that can cause:
- Occupational asthma – Isocyanates, flour dust, welding fumes
- Dermatitis – Cement, cleaning agents, industrial oils
- Lung disease – Silica, asbestos, wood dust
Testing and Re-Evaluation
- Baseline health checks upon employment
- Annual lung function tests for workers in high-risk areas
- Dermatitis screening every six months for employees handling irritants
Maintain confidential health records and ensure employees understand their right to report symptoms early to prevent long-term harm.
Health Surveillance Requirements: COSHH health surveillance – COSHH
Regulation 12 – Training and Information for Employees
Employers must ensure all workers understand:
- The hazards they may be exposed to
- How to use PPE correctly
- Proper chemical handling, storage, and disposal procedures
- Emergency response procedures
Refresher Training Requirements
- Annual COSHH training for all employees
- Immediate training when new substances are introduced
- Practical, hands-on PPE training every six months
HSE Guide on COSHH Training: Training for employees working with substances hazardous…
Regulation 13 – Safe Disposal of Hazardous Substances
Employers must ensure that hazardous substances are disposed of safely by:
- Labelling and segregating hazardous waste
- Using licensed hazardous waste disposal companies
- Storing waste safely before disposal
Timing and Record-Keeping
- Hazardous waste must be removed at least every three months
- Disposal records must be kept for three years
Hazardous Waste Disposal Guide: Hazardous waste: Overview – GOV.UK
How to Ensure COSHH Compliance
Step 1: Conduct and Update COSHH Risk Assessments
- Review at least annually or after workplace changes
- Train employees on risk factors
Step 2: Implement Control Measures and Re-Evaluate Their Effectiveness
- Engineering controls tested every 14 months
- PPE fit-tested annually
Step 3: Train Employees and Schedule Refresher Training
- COSHH awareness training annually
- PPE practical sessions every six months
Step 4: Monitor Exposure Levels and Conduct Regular Health Surveillance
- Air quality checks annually
- Health surveillance every six months or annually depending on risk
Step 5: Maintain and Inspect Safety Equipment Regularly
- LEV and ventilation testing at least every 14 months
- PPE checked before every use
We made it. The wrap up.
COSHH compliance is a continuous process, requiring risk assessment, control implementation, regular testing, and employee education. Employers must ensure hazardous substances are managed effectively and that employees are well-informed and protected.
For further guidance, refer to official HSE resources or consult a workplace safety professional.
COSHH Overview by HSE: Control of Substances Hazardous to Health (COSHH) – HSE
Disclaimer:
The information provided on this site is for general informational purposes only and may not reflect the most current regulations or standards. Legislation, industry guidelines, and best practices can change over time, and it is the user’s responsibility to research and ensure compliance with the latest requirements for their specific situation. Always consult a qualified professional for advice tailored to your project or application.