Flash Testing vs. Insulation Resistance Testing
In the electrical industry, misconceptions about testing methods can lead to unsafe practices, non-compliance, or even damage to sensitive equipment.
One of the most common misunderstandings is the belief that a Flash Test (Power-Frequency Withstand Voltage Test) and an Insulation Resistance Test (IR Test) are interchangeable. This confusion is often exacerbated by the availability of high-voltage insulation testers (commonly branded as “Megger“).
I had better just mention at this point the text below relates to the UK but BS and IEC run together and are much alike.
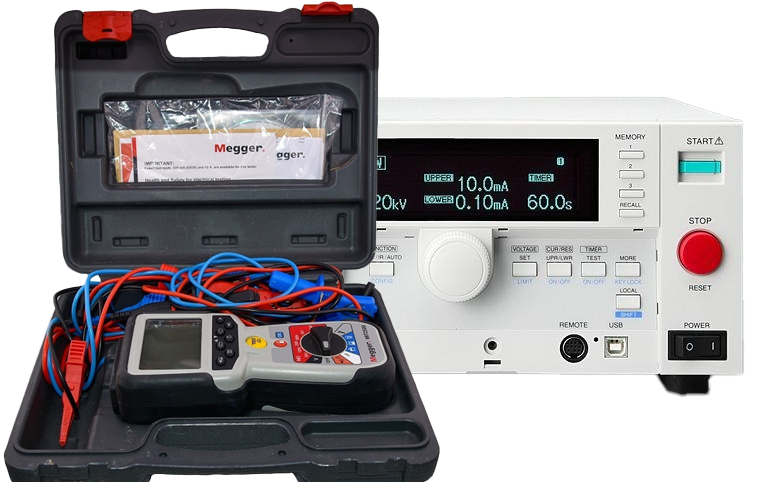
Context for BS and IEC
IEC Standards: Published by the International Electrotechnical Commission (IEC), they provide a global framework for electrical and electronic standards.
BS Standards: Published by British Standards Institution (BSI), BS standards often adopt IEC standards verbatim but add a national foreword or annex where necessary.
In the UK, most BS EN standards are direct adoptions of IEC standards through CENELEC (European Committee for Electrotechnical Standardisation).
BS EN 61439-1: This is the British adoption of IEC 61439-1, which defines the general requirements for low-voltage switchgear and control gear assemblies.
The content of the standard is technically identical, ensuring compliance with both standards provides the same level of safety and performance.
Apologies for going off track.
With that out of the way this page will hopefully explain differences between these two essential tests, their purposes, and why it’s vital to apply the correct method for the right situation. We’ll also delve into how BS EN 61439-1 governs the requirements for main and auxiliary circuits, ensuring safety and compliance.
What Is a Flash Test? The Role of Dielectric Strength in Electrical Safety
The Flash Test, also known as the Power-Frequency Withstand Voltage Test, is a type of dielectric test. It evaluates an electrical system’s ability to withstand high-voltage AC stress without breaking down. This test is crucial for ensuring the system can handle extreme events such as lightning strikes, switching surges, and fault conditions.
Key Features of Flash Testing
- High Voltage Application
- Voltage levels typically range from 1,890V to 2,500V AC for systems with nominal voltages between 300V and 600V.
- The test applies this voltage between live conductors and earth or between conductors.
- Leakage Current Monitoring
- Measures the leakage current in milliamps (mA).
- According to BS EN 61439-1, the leakage current must remain below 3.5mA for a successful test.
- Duration
- 1 second for routine on-site testing. That is a ramp up to the voltage and not immediate applied voltage. Should it warrant it possibly 5 seconds (Unofficially). 1 second given the size of DUT (Device Under Test) may not be long enough for a stable reading.
- 60 seconds for type testing in factory-controlled environments, as recommended by BEAMA. Similar fashion a ramped / applied voltage.
- Purpose
- Detects manufacturing defects, insulation weaknesses, or contamination.
- Validates the system’s ability to withstand transient overvoltage conditions.
Understanding Dielectric Properties
The core principle behind flash testing is dielectric strength—the maximum electric field an insulating material can withstand without failure. Here’s how it works:
- Creating an Electric Field
When high AC voltage is applied, it generates an electric field across the insulation. The field strength depends on the applied voltage and the material’s dielectric constant. - Leakage Current Components
Leakage current consists of:- Resistive Leakage: Due to the finite electrical resistance of the insulation.
- Capacitive Leakage: Arising from the capacitive nature of insulation in AC systems.
What Is Resistive Leakage?
Resistive leakage is a component of the total leakage current in an electrical system. It arises from the inherent electrical resistance of the insulation material. Unlike capacitive leakage, which results from the system’s capacitance, resistive leakage is directly related to the quality and condition of the insulation.
Causes of Resistive Leakage
- Material Imperfections
All insulation materials have finite resistance. Tiny imperfections, such as microcracks or impurities, can create pathways for current to flow. - Environmental Factors
- Moisture Ingress: Water reduces the insulation resistance, increasing resistive leakage.
- Contaminants: Dust, oil, or other contaminants on the insulation surface can form conductive paths.
- Ageing and Degradation: Over time, insulation materials can deteriorate, reducing resistance.
- Surface Tracking
Surface tracking occurs when contaminants on the insulation create a partial conductive path, allowing current to flow along the surface.
Why Is Resistive Leakage Important?
Resistive leakage is a critical parameter in both flash testing and insulation resistance testing. High levels of resistive leakage can indicate degraded or contaminated insulation, which may compromise the system’s safety and reliability. In flash testing, resistive leakage contributes to the overall leakage current, and its value must stay below the prescribed threshold (e.g., 3.5mA).
What Is Capacitive Leakage?
Definition and Causes
Capacitive leakage occurs because insulation between conductors acts like a capacitor. When AC voltage is applied, the alternating electric field induces a displacement current through the insulation, even if it’s in perfect condition.
Factors Affecting Capacitive Leakage
- Geometry of Conductors: Larger surface areas and shorter distances increase capacitance.
- Dielectric Constant: Materials with higher dielectric constants exhibit greater capacitance.
- Frequency of Applied Voltage: Higher frequencies lead to increased capacitive leakage.
Impact of Capacitive Leakage on Flash Testing
- Natural Leakage in High-Quality Insulation
Even in systems with perfect insulation, capacitive leakage will be present during a flash test. This current is non-destructive and expected, but it must remain below the defined 3.5mA threshold. - Misinterpretation of Results
An engineer unfamiliar with capacitive leakage may incorrectly interpret the presence of this current as a sign of insulation failure. Understanding its role is crucial for accurately assessing test results. - Relevance to Testing High-Capacitance Systems
In systems with long cables or large busbars, the capacitance increases, leading to higher capacitive leakage currents. Flash testers account for this by isolating and measuring both the resistive and capacitive components of leakage current.
So here’s a flash test related catch up.
- Higher Voltage, Increased Stress
The applied voltage in a flash test is significantly higher than the system’s nominal operating voltage. This high stress may reveal insulation weaknesses that would not manifest under normal operating conditions. - Combined Leakage Components
Resistive leakage combines with capacitive leakage in AC systems, resulting in a total measured leakage current. However, resistive leakage remains an essential indicator of the insulation’s quality. - Measurement
- Measured in milliamps (mA) as part of the total leakage current.
- Must remain below a threshold (e.g., 3.5mA) as specified in BS EN 61439-1.
What Is an Insulation Resistance Test?
An Insulation Resistance Test assesses the insulation’s ability to resist current flow under normal operating conditions. It uses DC voltage, which eliminates the capacitive effects present in AC systems, making it ideal for measuring the insulation’s resistive properties.
Key Features of Insulation Resistance Testing
- Lower Voltage Application
- Commonly performed at 500V DC, though high-end testers can apply up to 2kV DC.
- Focuses solely on resistive leakage, ignoring capacitive effects.
- Resistance Measurement
- Results are displayed in megaohms (MΩ).
- A resistance of ≥ 1 MΩ is typically required for a pass.
- Purpose
- Detects moisture ingress, contamination, and age-related degradation.
- Ensures the system’s long-term reliability.
Looking Inside Insulation Resistance Testing
Here’s what happens during an insulation resistance test:
Direct Current Flow
DC voltage forces current through the insulation, allowing only resistive pathways to conduct.
Leakage Pathways
Leakage increases if the insulation is compromised by moisture, dust, or material deterioration.
Resistive Leakage in Flash Testing vs. Insulation Resistance Testing
While resistive leakage is a concept present in both Flash Testing and Insulation Resistance (IR) Testing, it behaves differently in each context due to the nature of the tests and the voltages applied.
Resistive Leakage in Flash Testing
In a Flash Test (Power-Frequency Withstand Voltage Test), resistive leakage refers to the current that flows through the insulation under high AC voltage conditions. This current is part of the total leakage current, which also includes capacitive leakage. Flash testing applies a high voltage (e.g., 2,500V AC) at the system’s operating frequency (typically 50Hz in the UK).
Resistive Leakage in Insulation Resistance Testing
In an Insulation Resistance Test, only resistive leakage is considered because the test uses DC voltage. By eliminating the effects of capacitance, the test provides a clearer measure of the insulation’s resistive properties.
Breakdown
- Lower Voltage, Less Stress
The voltage applied during an IR test is typically 500V DC, much lower than the voltage used in flash testing. This reduces the stress on the insulation, making it safer for sensitive components. - No Capacitive Leakage
Since DC voltage is used, the capacitive component of leakage current is eliminated. The test focuses solely on resistive leakage, providing a straightforward measure of the insulation’s resistance. - Measurement
- Resistance is measured in megaohms (MΩ).
- A typical pass threshold is ≥ 1 MΩ, indicating good insulation.
Flash Testing vs. Insulation Resistance Testing: Key Differences
Aspect | Flash Test (Dielectric Test) | Insulation Resistance Test |
---|---|---|
Voltage Type | High AC Voltage | DC Voltage |
Typical Voltage Levels | 1,890V – 2,500V AC | 500V – 2kV DC |
Leakage Current Measurement | Yes (in mA) | No, measures resistance (in MΩ) |
Purpose | Tests dielectric strength under extreme conditions | Measures insulation health under normal conditions |
Application | Main Circuits, transient overvoltage simulation | Auxiliary Circuits, long-term reliability |
Why an IR Tester Cannot Replace a Flash Tester
Some engineers mistakenly believe that a high-voltage IR tester (e.g., a 2kV Megger) can substitute for a flash tester. However, these devices serve different purposes:
- Flash Testers apply high AC voltage at power frequency to simulate real-world overvoltage conditions, measuring leakage current in mA.
- Insulation Resistance Testers measure resistive leakage in MΩ using DC voltage, making them ideal for routine checks but insufficient for dielectric strength validation.
Best Practices for Electrical Testing
- Know Your Circuit Type
- Main Circuits: Require flash testing.
- Auxiliary Circuits: Insulation resistance testing is sufficient unless they handle >16A.
- Follow Manufacturer Guidelines
Devices like ACBs and ATS units may have sensitive electronics that could be damaged during flash testing. Always consult manufacturer recommendations. - Use the Right Equipment
- Flash Testers for dielectric testing.
- IR Testers for auxiliary circuits and sensitive electronics.
Phew we made it. Smoke and mirrors be gone.
Flash testing and insulation resistance testing are indispensable tools, but they serve different purposes. Using an IR tester in place of a flash tester risks non-compliance with BS EN 61439-1, compromising safety and system integrity.
By understanding the differences and applying the correct testing methods, we can ensure reliable, compliant, and safe electrical systems. For further guidance, consult the relevant clauses in BS EN 61439-1 or reach out to a switchgear specialist.
Disclaimer:
The information provided on this site is for general informational purposes only and may not reflect the most current regulations or standards. Legislation, industry guidelines, and best practices can change over time, and it is the user’s responsibility to research and ensure compliance with the latest requirements for their specific situation. Always consult a qualified professional for advice tailored to your project or application.